SPC Flooring is a popular flooring material for many commercial applications for many of the same reasons it is so popular for residential applications. It is water-resistant and low maintenance, which helps to control upkeep costs, and it is relatively durable so you will not have to replace it very often. It is also available in a wide variety of colors, textures, and style options. It can even be printed to simulate the look of hardwood, stone, or carpet.
When it comes to commercial SPC flooring, you get what you pay for. The quality of the material that you purchase will have a direct impact on how well it will withstand the rigors of varying levels of foot traffic.
With SPC flooring, the colors are homogenous through the entire piece of material dimensionally, so you don’t have to worry about them fading away through wear.
Commercial SPC Flooring Warranties
In many cases, the residential and commercial warranty on materials will vary. Make sure that the distributor knows the level of traffic that you are expecting so that they can accurately adjust the warranty to your specific situation.
Remember that the warranty only covers manufacturer defects. These are most often misprints of colors or sheets and tiles that do not line up properly. It does not cover installation mistakes, which are the most common cause of SPC flooring problems later.
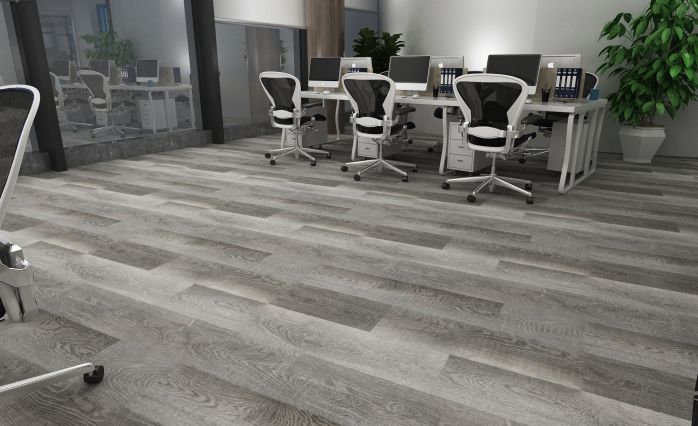
Long-Term Issues With Commercial SPC Floors
+Dull surface
Dulling of the SPC’s surface finish is probably the most common long-term issue with commercial product installation. This is caused by small pieces of dirt, sand, and debris being tracked across the floor by shoes and the wind. As these tiny particles scrape across the floor, they act like the grits of a piece of sandpaper, scratching and marring the surface of the SPC.
Solutions: The easiest way to prevent dulling of your SPC floors is to keep them free of those tiny particles that can harm them. Sweeping, vacuuming, or mopping periodically can do a lot to help protect a SPC floor in a high-traffic area. The use of floor mats at entrances and exterior doorways can also help to trap some of the debris before it can get inside where it can harm.
+ Discoloration
Discoloration of commercial SPC floors can happen over time due to the buildup of dirt, oil, and others. The rubber in some shoes can even cause slight discolorations on the floor. Prolonged exposure to heat or direct sunlight will also discolor the material, causing it to take on a yellowish color.
Solutions: Regular cleaning will help to remove the oils and greases that can discolor dercorative film over time. Floor mats set at entrances and exits will also help to cut down on mud and other staining agents that get tracked in. The use of curtains in places where windows and glass doors shine direct sunlight down on the floor can help prevent yellowing effects. However, SPC floors should not be installed in areas of high heat output, such as near heating ducts and vents.
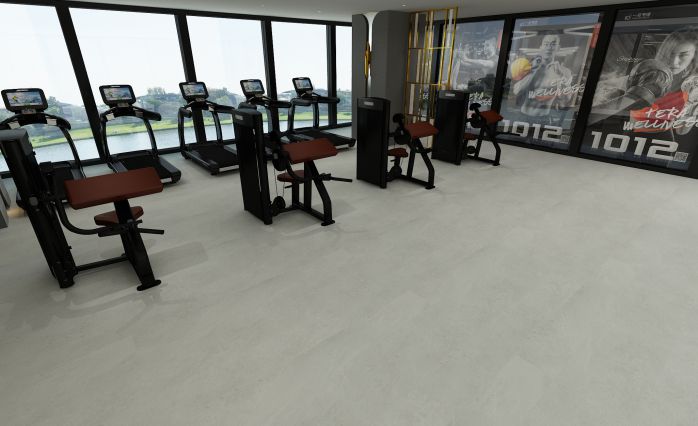
+ Surface Dents and Damage
Surface dents and damage to the floor can be caused by a variety of issues. Heavy furniture scraping across the floor can cause gouges and scratches. Sharp unprotected chair legs can also severely mar a commercial SPC floor in a cafeteria or eating area. Even some unpadded high heels can cause damage to the floor’s surface.
Solutions: If the scratches and dents are small, then you can use liquid seam filler to repair them. Make sure that the SPC is clean and dry, and then apply a small amount of the clear liquid to the blemish, being sure to smooth it out so it does not create bubbles or mounds. As it dries, it should cause smaller blemishes to vanish.
With SPC plank, you have the option of removing the affected area and replacing it with a matched patch.